GehäuseTechnologie.
Gehäuse-
Technologie
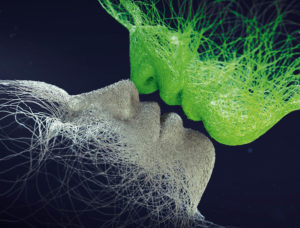
Kunststoffgehäuse im Präzisionsspritzguss hergestellt.
Miniaturisierte Sensorik ist empfindlich und muss daher vor äußeren Einflüssen und mechanischen Beschädigungen geschützt werden. Dazu stellt 2E mechatronic in vollautomatischen Prozessen hochwertige Sensorgehäuse mit höchster Präzision her. Zusätzlich können die Produkte dank modernster Gehäusetechnologie in Bezug auf umspritzte Einlegeteile wie Buchsen, Pins, etc. an nahezu alle Kundenwünsche angepasst werden.
E-Mail: info@2e-mechatronic.de Phone: +49 (0)7021 / 93010
NOx Sensoren sind Teil von Abgasnachbehandlungssystemen bei Fahrzeugen. Als NOx werden verschiedene gasförmige Oxide des Stickstoffs bezeichnet, die unter anderem bei der Verbrennung von fossilen Brennstoffen entstehen.
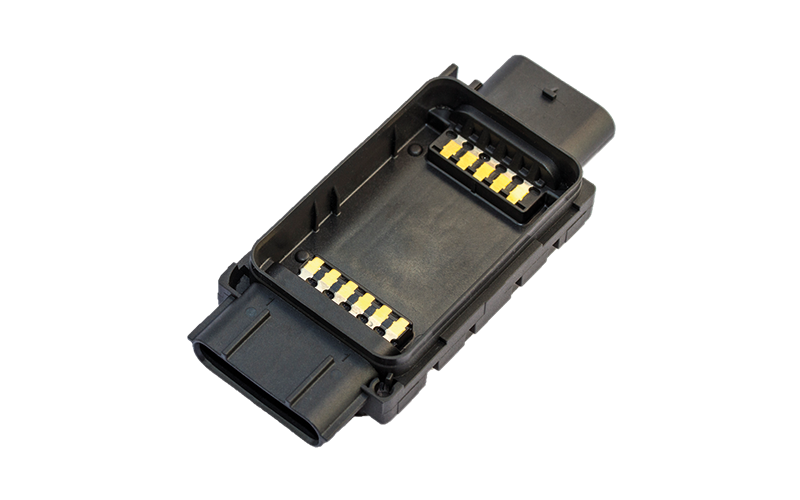
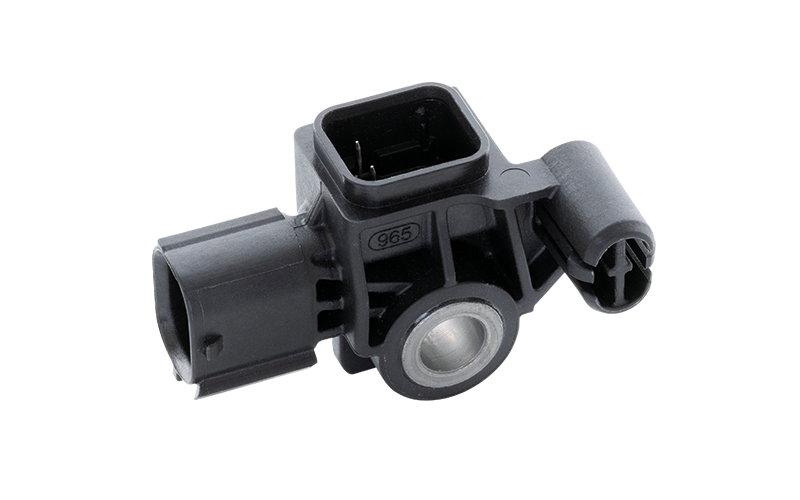
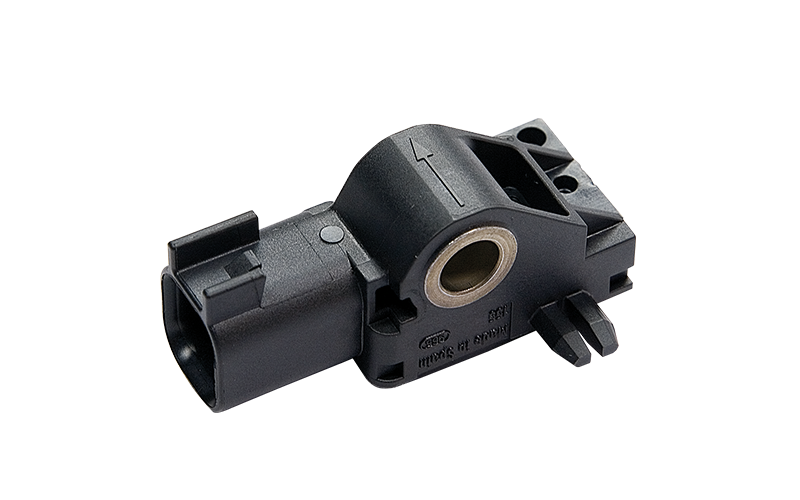
Diese Variante von Gehäusen für Beschleunigungssensoren dient zur Aufnahme kleinster Elektronik, die im Fahrzeug lagerichtigt angebracht werden muss. Die Verbindung zur Elektronik erfolgt mittels Press-Fit-Technologie.
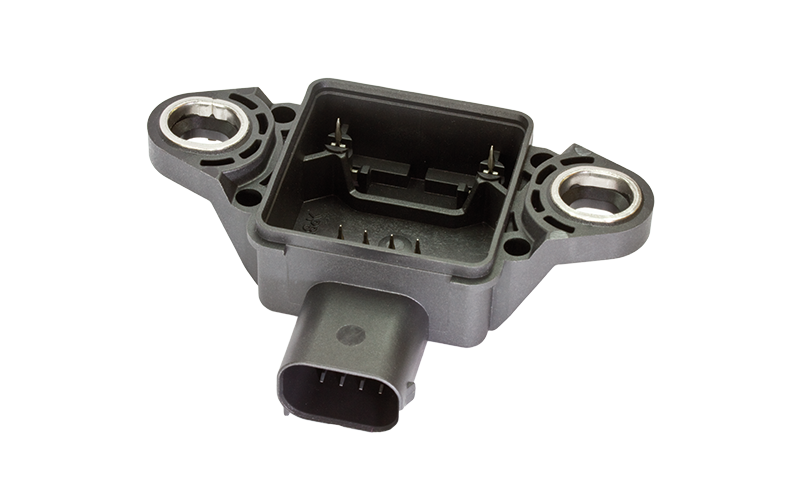
Drehratensensoren sind Bestandteil von Fahrassistenzsystemen, in diesem Fall des sog. ESP® (Electronic Stability Control), auf Deutsch: Elektronisches Stabilitätsprogramm.
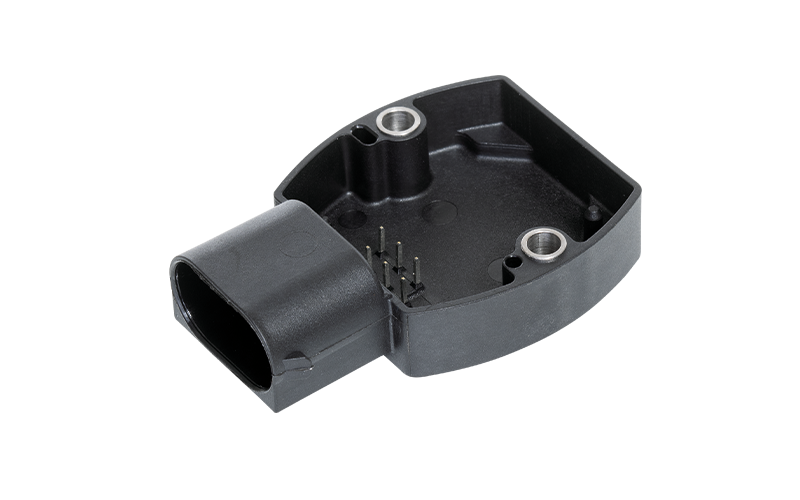
Der magnetische Winkelsensor mit kontaktlosem Hall-Effekt-Messprinzip wird unter anderem bei mobilen Land- und Baumaschinen eingesetzt.

Die Start-Stopp-Automatik wird unter anderem bei Nutzfahrzeugen eingesetzt. Bei häufigen Stopps werden Verbrauch und CO2-Emissionen reduziert.
WissenswerTes
Ablauf eines Fertigungsprozesses für ein Kunststoffgehäuse
Grob lässt sich der Fertigungsprozess der Sensorgehäuse in vier bis fünf Schritte einteilen. Im ersten Schritt werden die individuellen Teile (Pins, Buchsen, etc.) in das Spritzgusswerkzeug eingesetzt. Anschließend folgt das Umspritzen der Teile im Präzisionsspritzguss. Durch die gewählte Anlagentechnik kann die Prozesszeit in der Spritzgießmaschine um bis zu 40% reduziert werden. Je nach Anforderung können nach dem Umspritzen weitere Fertigungsschritte notwendig sein, wie z.B. das Anbringen eines Druckausgleichselements, etc. Der vorletzte Schritt besteht aus verschiedenen Prüfungen. Geprüft wird unter anderem die Vollständigkeit der Einlegeteile, Dichtheit, Maßhaltigkeit, Sauberkeit und Kurzschluss mittels unterschiedlichster Prüftechniken. Im letzten Schritt werden die Sensorgehäuse in KLTs verpackt. Natürlich können auch an geeigneten Stellen im Ablauf Vor- und Nachbehandlungsprozesse wie beispielsweise Reinigen integriert werden. Die vollautomatische Herstellung hat den Vorteil, dass Abweichungen minimiert werden. Einmal justierte Prozesse können mit einer enormen Präzision in sehr großen Stückzahlen ausgeführt werden. Kontinuierliche Verbesserungspotenziale z.B. in der Prüftechnik werden dabei bauteilunabhängig umgesetzt. Ein hervorragendes Beispiel für moderne Gehäusetechnologie ist das Gehäuse für Drehratensensoren MM5/MM7 mit Abmessungen von gerade einmal 54 x 80 x 21 mm.
Kunststoffgehäuse der Extraklasse - Materialien und Eigenschaften
Einer der meist genutzten Stoffe ist Polybutylenterephthalat, kurz PBT. Dieser Kunststoff lässt sich bei einer hohen Maßhaltigkeit sehr gut verarbeiten und verfügt über eine hohe Temperaturbeständigkeit. Letztere macht ihn für die großen Temperaturunterschiede im Auto zum idealen Werkstoff. Spezielle Typen werden dabei für bestimmte Anforderungen ausgewählt, z.B. fließoptimierte bei feineren Konturen, hydrolysestabilisierte für feuchtere Umgebungen und natürlich laserbeschriftbare Typen. Daneben werden von uns natürlich nahezu alle technischen Kunststoffe verarbeitet. Die hohe Festigkeit und Widerstandskraft gegen mechanischen Verschleiß erlaubt dem Werkstoff, den Vibrationen in Fahrzeugen über lange Zeit Stand zu halten. Weiterhin verfügt PBT über eine gute chemische Widerstandsfähigkeit gegen die meisten Lösungsmittel.
Die Anlagen, Werkzeuge und Einlegeteile werden von zertifizierten Spezialisten kundenspezifisch in der benötigten Qualität angefertigt. Wichtig für uns ist auch eine kurze Reaktionszeit um die Liefersicherheit aufrecht erhalten zu können. Unser Lieferantennetzwerk vereint diese Stärken.
Wir verarbeiten standardmäßig Kontakte mit Einpresszone (Pressfit-Technologie), Lötanschlüssen und Bondflächen. Diese können bei uns als Schüttgut oder am Band direkt an der Anlage gebogen, getrennt und eingesetzt werden. Gedrehte und stanzgerollte Buchsen aus den verschiedensten Werkstoffen und Oberflächen kommen zum Einsatz. Diese werden üblicherweise mittels Vibrationswendelförderer für die Weiterverarbeitung bereitgestellt. Andere Bereitstellungsformen können natürlich ebenfalls verarbeitet werden. Im Spritzgießprozess verwenden wir Werkstückträgerkonzepte oder Drehtellermaschinen. Viele Spritzgießwerkzeuge sind mit Wechseleinsätzen variantenfähig. Hinsichtlich vor- und nachgelagerter Prozesse und Prüfungen kann alles integriert werden, was sich automatisieren lässt. Um nur einige Beispiele zu nennen: Überdruckprüfung, elektrischer Durchgang, Hochspannungsprüfung, Ultraschallschweißen oder Kleben von Druckausgleichselementen, Laserbeschriftung, automatische optische Inspektion (z.B. Bondflächenprüfung), Schweißvorgänge, Reinigung…
Sprechen Sie uns an, wir finden eine Lösung!
Anwendungsbereiche der 2E mechatronic Gehäusetechnologie
Die individuell gefertigten Gehäuse kommen überwiegend in der Automobilindustrie zum Einsatz. Als zertifizierter Zulieferer nach IATF 16949 werden in jedem Prozess die Anforderungen an die Qualität erfüllt. Beispiele sind die Herstellung von Gehäusen für
• Drehratensensoren als Teil des ESP©
• Anlasssteuerungen für Start-Stopp-Systeme
• NOx Sensoren als Teil des Abgassystems
• Seitenairbagsensoren.